With the development of freeze-drying technology, vacuum freeze-drying machines are widely used in fields such as biology, medicine, and the preparation of nanomaterials. Due to the working characteristics of vacuum freeze-drying machines (Mr. Sheng 13372267977), vacuum freeze-drying machines often operate beyond their limits, which leads to frequent malfunctions in the refrigeration system, which is the core component of vacuum freeze-drying machines. Most refrigeration machines are composed of compressors, evaporators, condensers, expansion valves, gas-liquid separators, oil separators, and other components. In order to reduce the occurrence of faults in the refrigeration system of vacuum freeze-drying machines, it is necessary to have an understanding of some common faults, master the solutions to these faults, and understand the daily maintenance and upkeep of the refrigeration system of vacuum freeze-drying machines, in order to reduce the occurrence of faults in the refrigeration system of vacuum freeze-drying machines. Starting from the common problems in the refrigeration system of vacuum freeze-drying machines, a specific analysis of relevant solutions was conducted, And a summary was made on the daily maintenance and upkeep of the refrigeration system of the vacuum freeze dryer.
Several common faults in the refrigeration system of vacuum freeze-drying machines include: high pressure alarm, compressor motor overload, motor temperature too high, oil pressure difference alarm, water pressure alarm, and the effectiveness of expansion valve adjustment. Xinyu freeze-drying analyzes the causes and related solutions of these faults. The causes of six types of faults and their solutions are as follows: (1) For the occurrence of high-pressure alarms, the reasons are generally as follows: insufficient water volume in the water-cooled condenser or excessively high water temperature; Some scale has formed inside the water-cooled condenser, which reduces the efficiency of heat conversion; The low-pressure pipeline of the compressor ruptured during operation, causing air to enter the refrigeration pipeline; The valve of the refrigeration pipeline is not fully opened, or the exhaust pipeline is blocked, causing poor exhaust flow; Too much use of the refrigerator leads to excessive exhaust pressure. The solution is to reduce the water temperature or increase the flow rate; Clean the water condenser; The refrigeration pipeline needs to be simplified. If this operation cannot be carried out while in operation, the shut-off valve above the water condenser can be opened first to release some of the air from the water condenser; It is necessary to open the valve on the compressor pipeline to its maximum position; A portion of the refrigeration unit needs to be discharged.
(2) For the occurrence of overloading of the compressor motor, the reason may be: there are debris in the piston cylinder, causing the piston to not move smoothly, resulting in the occurrence of holding the shaft and closing the cylinder; The thermal load of the compressor is overloaded, which may be caused by operations such as steam sterilization; The relay for thermal overload did not reset in a timely manner. The solution is to promptly clean the internal residue of the compressor; Timely cool the compressor to the allowable temperature; Reset the relay in a timely manner.
(3) For the occurrence of high motor temperature, the reason may be that the refrigeration unit has insufficient air return, resulting in insufficient cooling of the motor; Insufficient or missing refrigeration unit; Caused by unstable three-phase power supply of the compressor; The thermal protection module of the compressor has malfunctioned; The liquid supply pipeline is blocked. The solution is to restart the switch of the compressor; Timely replenish refrigerant; Provide power to the compressor as required; Timely evacuate the blocked area
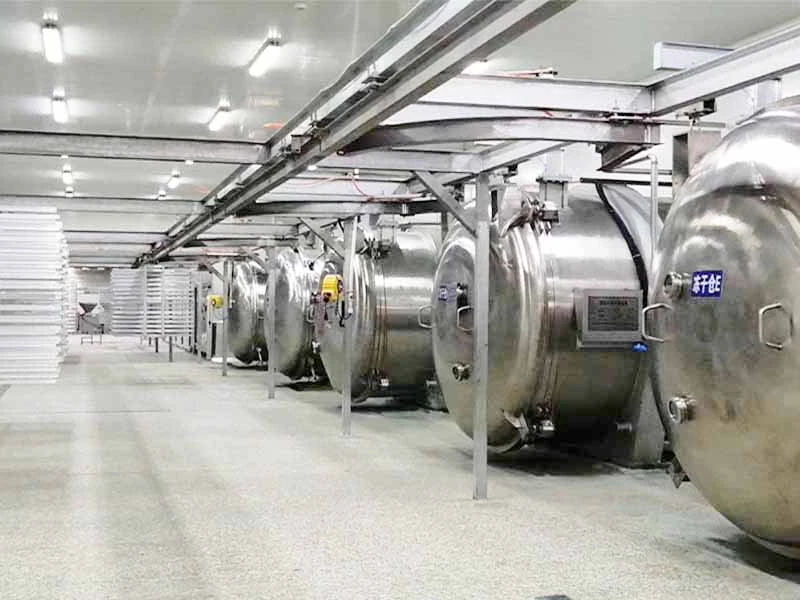